آلومینا زیرکونیا - ویکیپدیا، دانشنامهٔ آزاد
این مقاله نیازمند ویکیسازی است. لطفاً با توجه به راهنمای ویرایش و شیوهنامه، محتوای آن را بهبود بخشید. (اکتبر ۲۰۱۸) |
کامپوزیتهای آلومینا زیرکونیا ترکیبی از اکسید آلومینیوم با اکسید زیرکونیوم بوده و جزو کامپوزیتهای سرامیکی است که به دلیل خواص مکانیکی خوبی که دارند مورد توجه هستند. این کامپوزیتها بهطور معمول در ابزارهای برش و سایندهها که نیاز به سختی و استحکام بسیار بالا در کنار چقرمگی شکست بالا و مطلوب است استفاده میشوند و همچنین به دلیل زیست سازگاری بالا الومینا و زیرکونیا همراه با خواص مکانیکی خوب و واکنش پذیری بسیار کم کاربردهای پزشکی بسیاری دارند.[۱]
معرفی[ویرایش]
ریزساختار کامپوزیتهای آلومینا/زیرکونیا بر پایه حضور دو فاز جداگانه، بدون انجام واکنش و تشکیل محلول جامد میان این دو بنا شدهاست. براساس دیاگرام فاز این دو اکسید مقدار کم به عنوان یک افزودنی به باعث تشکیل محلول جامد و در نتیجه افزایش تراکم پذیری کامپوزیتهای پایه الومینا میگردد.[۲]

همچنین حضور ذرات در نمونههای بهطور جدی رشد دانه را محدود میکند و سرعت رشد ذرات بسیار کمتر از نمونههای فاقد ZrO2 است و به عبارتی ذرات زیرکونیا از رشد بیش از حد و افراطی ذرات الومینا جلوگیری میکند.[۳]
حضور ذرات زیرکونیا در زمینه آلومینا، به عنوان ذرات مجزا که قابلیت انجام دگرگونی فازی را دارند، سازوکار اصلی افزایش چقرمگی در کامپوزیتهای آلومینا/زیرکونیا است.[۴] در حقیقت این دگرگونی فازی سبب ایجاد ریز ترک و ایجاد تنش فشاری در سطح و انحراف ترک خواهد شد.[۵][۶] کامپوزیت آلومینا/زیرکونیا، سختی بالا آلومینا و مقاومت شکست عالی زیرکونیا را با هم ترکیب کرده و به عنوان یک جایگزین مؤثر برای زیرکونیا منوکلینیک و آلومینا در طیف گستردهای از کاربردها گسترده شدهاست.[۷][۸] در واقع، نقص اصلی زیرکونیا مونوکلینیک پیری آن به علت استحاله فازی تتراگونال به مونوکلینیک وقتی در معرض شرایط هیدروترمال قرار میگیرد است. از سوی دیگر مطالعات متعددی نیز نشان دادند شکست سرامیک یکپارچه آلومینا به علت مقاومت کم ان در مقابل انتشار ترک است. کامپوزیت آلومینا و زیرکونیا این اثرات را از بین میبرد. دو دسته کامپوزیت بر اساس سیستم ساخته شده و به صورت تجاری استفاده شده:[۹][۱۰] آلومینای چقر شده با ذرات زیرکونیا (ZTA) و زیرکونیای تقویت شده با ذرات آلومینا (ATZ).
دسته اول الومینای تقویت شده با ۱۰ تا ۲۰ درصد وزنی زیرکونیا و دسته دوم عموماً زیرکونیای تثبیت شده با ایتریا به همراه تقریباً ۲۰ درصد وزنی الومینا است.
در سال ۱۹۷۵ گارویه و همکارانش[۱۱] اولین کسانی بودند که توانائی بالای زیرکونیا را برای بهبود خواص مکانیکی آلومینا کشف کردند حضور ذرات زیرکونیا در ساختار آلومینا میتواند همچون سدی از رشد ترکهای موجود در ساختار جلوگیری کند. علاوه بر آن درصورتی که از فاز تتراگونال پایدار شده زیرکنیا به عنوان ذرات پخش شونده استفاده گردد به هنگام برخورد ترکهای در حال رشد به این ذرات، انرژی ترک صرف تبدیل فاز تتراگونال به منوکلینیک گردیده و لذا رشد ترک کند یا متوقف میگردد. همچنین گارویه گزارش داد که اندازه ذرات تتراگونال پایدار شده زیرکونیا باید از یک حد بحرانی کوچکتر نگه داشته شود تا بتوان به مقادیر بالایی از چقرمگی شکست دست یافت.[۱۱] به عبارتی ذرات تتراگونال زیرکونیا باید به حدی کوچک نگاه داشته شوند که به صورت خود بخودی در ماتریس زیرکونیا مکعبی تغییر فرم پیدا نکرده و تنها در اثر اعمال تنش به آنها این تغییر فرم صورت گیرد.[۱۲]
ذرات زیرکونیا به عنوان یک عامل چقرمهکننده برای سرامیکها مورد استفاده قرار میگیرند و سرامیکهای چقرمه شده با زیرکونیا (ZTCS)بسیار مورد توجه قرار گرفتهاند که از مهمترین آنها آلومینای تقویت شده با زیرکونیا(ZTA)است که به زمینه آلومینایی ذرات زیرکونیایی فاز تتراگونال یا مونوکلینیک افزوده میشود.[۱۳] در ZTA ها این موضوع ثابت شدهاست که افزودن فاز دوم باعث بهبود خواص مکانیکی اصلی مثل استحکام خمشی و چقرمگی شکست میشود. چنین پیشرفتهایی این ماده را کاندید مناسبی برای کاربردهای مهندسی که نیاز به سختی و مقاومت به سایش بالا و چقرمگی شکست متوسط دارند، کردهاست.[۱۴] مطالعات اخیر نشان میدهند حضور همزمان ذرات زیرکونیا و فلز میتواند باعث بهبود خواص مکانیکی کامپوزیتهای زمینه آلومینایی شود در این راستا، مطالعاتی پیرامون کامپوزیتهایی همچون / / صورت گرفتهاست. از جمله خواصی که در این مطالعات مورد بررسی قرارگرفتهاند میتوان به استحکام، چقرمگی شکست، سختی و مقاومت به اکسیداسیون اشاره کرد. در مطالعات فوق، افزایش استحکام و چقرمگی کامپوزیت تقویت شده با ذرات زیرکونیا و فلز در مقایسه با آلومینای تک فاز مشاهده شدهاست. سختی این کامپوزیتها با توجه به پایینتر بودن سختی زیرکونیا و فلزات نسبت به آلومینا، کاهش یافتهاست و همچنین مقاومت به اکسیداسیون ذاتی آلومینا در اثر افزوده شدن ذرات فلزی و زیرکونیا کاهش مییابد. به هر حال لازم است شرایط بهینهای از خواص متفاوت با توجه به کاربرد کامپوزیت مورد نظر لحاظ شود.[۱۵]
مکانیزمهای چقرمه شدن کامپوزیت الومینا زیرکونیا[ویرایش]
افزایش حجم و کرنش برشی حاصل از تغییر فاز تتراگونال زیرکونیا سبب مکانیزمهای چقرمگی مختلفی در این کامپوزیتها میگردد از جمله: تنش القایی ناشی از تغییر فاز، ایجاد میکرو ترکها، ایجاد تنش فشاری در سطح و انحراف ترک. دو مکانیزم اول مکانیزمهای اصلی افزایش چقرمگی در کامپوزیتهای الومینازیرکونیا میباشند.
وقتی یک ترک تحت تنش گسترش مییابد، تنشهای کششی بزرگی در اطراف ترک به ویژه در منطقه نوک ترک به وجود میآید. این تنشها، فشارهای شبکه بر روی ذرات زیرکونیای تتراگونال را آزاد میکند و اگر به حد کافی بزرگ باشند تنش کششی خالصی بر ذرات وارد میکند که در نتیجه، تبدیل فاز تتراگونال به مونوکلینیک اتفاق میافتد. در اثر این تبدیل انبساط حجمی در ذرات ایجاد میشود که نتیجهٔ آن ایجاد کرنش فشاری در اطراف ذرات است. به دلیل ایجاد این تنشهای فشاری به ویژه روی نوک ترک، ترک بسته شده یا احتیاج به انرژی بیشتری برای گسترش پیدا میکند. در هر صورت تغییرات فازی ذرات زیرکونیا باعث جذب انرژی ترک و در نتیجه افزایش چقرمگی کامپوزیت میشود.[۱۴][۱۶]
فاز تتراگونال زیرکونیا در دمای زیر 1100 درجه سانتی گراد به مونوکلینیک تجزیه میگردد و بنابراین جهت پایدار ماندن فاز تتراگونال در دمای اتاق نیاز به استفاده از موادی است تا با انحلال در ساختار زیرکونیا از تجزیه و تغییر ساختار شبکه در دماهای زیر 1100 درجه سانتی گراد جلوگیری کنند برای این منظور از موادی از جمله ایتریا ،سریا و منیزیا استفاده میگردد که به آنها تثبیتکننده گفته میشود و به زیرکونیا شامل این مواد زیرکونیای پایدار شده جزئی(PSZ) نام دارد.[۱۷] این مواد با انحلال در شبکه زیرکونیا و تشکیل محلول جامد سبب جلوگیری از بازشدن شبکه و در واقع افزایش حجم ان شده و در نتیجه زیرکونیا تتراگونال در دمای پایین دارای تنش فشاری باقی مانده در ساختار است.بهطور معمول مقدار پایدارکنندهها مناسب برای پایداری ساختار تتراگونال در نوع افزودنی ایتریا دار در حدود 5.4-3 درصد مولی و در نوع سریا دار در حدود 12 درصد مولی است.
مکانیزم تنش القایی ناشی از استحاله فازی[ویرایش]
مکانیزم تنش القایی ناشی از استحاله فازی به میزان فاز تتراگونال در دسترس در دمای محیط بستگی دارد که سبب میشود با رسیدن ترک به فاز تتراگونال انرژی نوک ترک صرف تأمین انرژی لازم جهت رهاسازی فاز تتراگونال از تنش فشاری در ساختار ماتریس زیرکونیا و تبدیل ان به مونوکلینیک گردیده و با گرفته شدن انرژی ترک از رشد آن جلوگیری میشود.[۱۶]
مکانیزم ریز ترکها[ویرایش]
مکانیزم ریز ترکها نیز با صرف انرژی ترک در حال گسترش در انشعابات ریز ترکها سبب کاهش انرژی نوک ترک میشود در واقع انرژی ترک را از حد بحرانی که توانایی رشد را دارا باشد کاهش میدهد و از رشد ان جلوگیری میکند. این ریز ترکها حاصل از ان دسته از ذرات تتراگونال زیرکونیا میباشند که به دلیل بزرگتر بودن اندازه آنها از حد بحرانی در حین فرایند سرد شدن دچار تغییر فاز شده و به فاز مونوکلینیک در دما محیط تبدیل شدهاند و این ریز ترکها در اطراف فاز مونوکلینیک شکل میگیرد.[۱۶]
مکانیزم تنش فشاری سطح[ویرایش]
در مکانیزم تنش فشاری سطح که وجود این تنش در سطح ماده در واقع ناشی از همان وجود فاز تتراگونال زیرکونیا در دما محیط و تنش فشاری موجود در ماتریس زیرکونیا که ناشی از عدم استحاله فازی در دمای پایین است، در برخورد نوک ترک که دارای انرژی به صورت تنش کششی است با این تنش فشاری انرژی ترک از بین میرود.[۱۶]
مکانیزم انحراف ترک[ویرایش]
در مکانیزم انحراف ترک میتوان گفت که در هنگام رسیدن ترک به فاز ثانویه با چقرمگی شکست بیشتر ترک از مسیر اصلی منحرف شده و مجبور میشود این فاز را دور بزند و بنابراین با طی مسیر بیشتر انرژی آن کاسته و رشد ان محدود و متوقف میگردد.[۱۶]
فرایند ساخت کامپوزیت آلومینا زیرکونیا[ویرایش]
فرایند ساخت کامپوزیت آلومینا/زیرکونیا بهطور کلی به صورت زیر تقسیمبندی میشود:
۱. شیمیایی
۲. زینتر(تفجوشی)پودرها
روش ساخت شیمیایی خود شامل روشهای اختلاط برشی، سل-ژل و CVD میشود.[۱۸] مرسومترین فرایند تولید کامپوزیت آلومینا/زیرکونیا روش سل-ژل است. فرایند سل-ژل شامل مجموعه ای از واکنشهای شیمیایی تغییرناپذیر است که این واکنشها باعث تبدیل مولکولهای محلول هموژن اولیه به عنوان سل به یک مولکول سنگین سه بعدی پلیمری به عنوان ژل میشوند. در حقیقت جامد الاستیک به وجود آمده باعث پرشدن حجم محلول موجود میشود. آماده سازی ذرات در اندازه و مقیاس ریز مستلزم آماده سازی و فراهم کردن یک زمینه پیوسته از یک حلال است که به آن سل کلوییدی میگویند. در این روش معمولاً به یک سیستم دیسپرز بسیار ریز که دارای انرژی آزاد بسیار بالایی است جهت درهم شکستن و به هم ریختن ساختار جامد نیاز است. به دلیل ریز دانه بودن ذرات و در نتیجه افزایش سطح ویژه مواد و سیستمهای کلوییدی تمایل و گرایش به اگلومره شدن دارد که این امر ناشی از نیروهای جاذبه واندروالس بین ذرات و پایین بودن نیروهای دافعه برای عبور از سد انرژی ذاتی به وجود آمده در این فرایند است. بزرگی و مقدار این سد انرژی اگلومره شدن بستگی به تعادل نیروهای جاذبه و دافعه بین ذرات دارد. در فرایند سل-ژل انتقال سل به ژل اغلب به وسیله تغییر PH و یا تغییر غلظت محلول بدست می آید. مزیت اصلی فرایند سل-ژل در تولید محصولی باخلوص بالا و دست یافتن به ریزساختار یکنواخت در دمای پایین است. هر مولکول از نمکهای اولیه دارای سرعت واکنش مربوط به خودش است که این سرعت واکنش بستگی به شرایطی چون pH، غلظت، حلال و دما دارد.[۱۹][۲۰] مواد اولیه برای تولید کامپوزیت آلومینا/زیرکونیا شامل پودر آلومینا و زیرکونیا با خلوص بالا و اسید آمینوبنزن به عنوان دفلوکولانت است. مشخصات پودرها به وسیله دستگاه XRD و اندازه کریستالها با استفاده از رابطه شرر و سطح ویژه به کمک روش BET و زیرساختار آنها با استفاده از میکروسکوپ الکترونی روبشی(SEM) و TEM (میکروسکوپ الکترونی عبوری) بدست می آید.[۲۱]
نکته ای که باید به ان توجه کرد این است که در ساخت برخی مواد کامپوزیتی امکان وجود دو مرحله وجود دارد، مرحله اول تولید پودر با خلوص بالای مواد سازنده و پایههای ساختار کامپوزیت است و مرحله دوم ساخت قطعات کامپوزیتی با شکل و فرم مورد نظر از پودرهای اولیه. بنابراین روش سل ژل و یا روش الیاژ سازی مکانیکی (خردایش ذرات و خالص سازی با شستشو یا روشهای دیگر) منجر به تولید ذرات ریز و با خلوص بالای الومینا و زیرکونیا گردیده که در سل ژل مخلوط پودرها با هم حاصل میشود و در روش کانیکی پس از خالص سازی پودرها با هم مخلوط شده و در نهایت در هر دو روش نیاز به زینتر مخلوط پودرها جهت دستیابی به قطعه با دانسیته نزدیک به دانسیته تئوری است.
نکته دیگر که در ساخت کامپوزیتهای الومینا زیرکونیا بسیار حائز اهمیت است دستیابی به ساختار نهایی با کمترین میزان تخلخل و عیوب با دانسیته ای بسیار نزدیک دانسیته تئوری بین 98 تا 99.8 درصد و ساختار ریز دانه با یکنواختی ساختار بالا است زیر خواص مکانیکی مورد نظر بسیار به ساختار وابسته است و بنابراین در انتخاب روش تولید میبایست حتماً به این نکات توجه ویژه کرد.[۲۲]
فرایند سل- ژل[ویرایش]
در فرایند سل ژل جهت تهیه الومینا زیرکونیا بهطور معمول از نیترات اومینیوم Al(NO3)3 و کلرید زیرکونیا ZrOCl2به عنوان مواد اولیه استفاده میگردد، که برای دستیابی به هیدروژل در محلول امونیاک حل شده و پس از پیر سازی ژل حاصل را در اب جوشانده تا ترکیبات اضافی (یون کلر و یون نیترات) خارج شده و سپس در 40 درجه سانتی گراد خشک میکنند و در نهایت کلسیناسیون در دمای 900 درجه سانتی گراد جهت خروج ترکیبات الی باقی مانده انجام میشود و پس از ان بالمیل تر با گلولههای زیرکونیایی جهت مخلوط سازی و هموژن سازی انجام میگردد و در نهایت پودر حاصل در 4 درجه سانتی گراد مجدد خشک شده تا پودر نهایی حاصل شود.[۲۲]
در روشی دیگر با استفاده از یک بالمیل گلوله ای تر به مدت مشخص سوسپانسیونی از پودر زیرکونیا به همراه اسید آمینوبنزن(به عنوان دی فلوکولانت) در محیط آلی و به موازات آن بهطور همزمان سوسپانسیونی از آلومینا به همراه اسید آمینوبنزن در محیط آلی تهیه میشود. سپس سوسپانسیونها را با یکدیگر مخلوط کرده و مخلوط نهایی در یک بالمیل گلوله ای به مدت معین مخلوط میشود و بعد دوغاب حاصل درون خشک کن قرار داده میشود. در نهایت از پودر حاصل با استفاده از پرس تک محوره قطعات مورد نظر ساخته میشود و قطعه حاصل برای خروج ترکیبات آلی از بدنه تحت عملیات حرارتی قرار میگیرد. جهت اختلاط پودرها میتوان از آسیاب تر در محیط آبی یا محلولهای آلی به صورت مخلوط هموژن درآورد. مطالعات نشان داده است که استفاده از آب سبب تشکیل اگلومرههای سخت در حین فرایند خشک کردن میشود. درصورتی که استفاده از محیط اتانول سبب پایداری و دفلوکوله شدن ذرات میشود و از تشکیل اگلومرههای سخت جلوگیری میکند. همچنین باید توجه داشت که فرایند فوق در بالمیل حاوی گلولههای زیرکونیایی برای جلوگیری از ورود ناخالصی در مخلوط انجام میشود.[۲۳]
فرایند زینتر پودرها[ویرایش]
در این فرایند مواد اولیه که شامل پودر آلومینا و زیرکونیا باخلوص بالا است را با درصد مشخص به همراه روانکار و چسب درون آسیاب سیاره ای جهت اختلاط ریخته و برای این کار از گلولههای زیرکونیایی یا آلومینایی برای جلوگیری از ورود ناخالصی به مجموعه استفاده میکنیم. سپس با استفاده از پرس سرد هیدرواستاتیک برای تهیه قرص اولیه قطعه به پودرها فشار وارد میکنیم که قالب پرس متناسب با ابعاد مورد نظر قطعه متغیر خواهد بود. قطعات تولیدی را جهت انجام فرایند زینترینگ درون کوره با دمای حدود 1600-1400 درجه سانتی گراد قرار میدهیم.فرایند زینتر بسته به میزان دانسیته مورد نظر و همچنین کاربرد میتواند به صورت زینتر بدون فشار یا همراه پرس گرم ایزو استاتیک انجام گردد همچنین استفاده از روشهای زینتر جرقه پلاسما (SPS) که به دلیل زمان بسیار کم مانع از رشد دانه میشود نیز امکانپذیر است [۲۴]
خواص کامپوزیتهای آلومینا زیرکونیا[ویرایش]
در کامپوزیتهای آلومینا زیرکونیا بحث خواص مکانیکی از اهمیت ویژه ای برخوردار است. در این راستا تحقیقات بسیاری صورت گرفتهاست.همچنین این مواد به دلیل خواص زیست سازگار پذیری بالای الومینا و زیرکونیا و واکنش پذیری بسیار پایین این مواد به ویژه مقاومت به اکسیداسیون بالا آنها در کاربردهای پزشکی بسیار مورد توجه هستند.
خواص مکانیکی کامپوزیت های آلومینا زیرکونیا[ویرایش]
در بحث خواص مکانیکی پارامترهایی که بیشتر مد نظر است چقرمگی، استحکام شکست، مدول یانگ و سختی است.باید توجه شود که اندازهگیری خواص مکانیکی زمانی از اعتبار کافی برخوردار است که دانسیته قطعه کامپوزیتی الومینا زیرکونیا مورد بررسی به دانسیته تئوری بسیار نزدیک و بیشتر از 96 درصد باشد.
خواص کامپوزیتهای الومینا زیرکونیا به مقدار بسیار زیادی به عواملی از جمله درصد فازهای الومینا و زیرکونیا موجود در ساختار،اندازه دانههای الومینا زیرکونیا، نحوه توزیع و محل قرارگیری فاز ثانویه و دانسیته کامپوزیت و میزان تخلخل ساختار وابسته است.
در تحقیقات اخیر که توسط سسایلینا و همکارانش انجام شد، نشان دادند که در کامپوزیتهای آلومینا زیرکونیا، با افزودن زیرکونیا، چقرمگی شکست در محدوده بین 6.1MPa.√m تا 7.16MPa.√m تغییر میکند. در رابطه با استحکام خمشی، مقادیر این پارامتر در محدوده 396.71MPa تا 736.55MPa متغیر است.
نتایج حاصل از این تحقیق در جدول زیر آورده شدهاست.[۲۵]
استحکام خمشی (MPa) | KIC (MPa.m1/2) | مدول یانگ(GPa) | HV(GPa) | مواد |
---|---|---|---|---|
396.71 | 6.10 | 380.00 | 0.52 ± 17.53 | A |
441.40 | 6.38 | 365.22 | 0.76 ± 17.53 | 5ZT |
473.13 | 6.43 | 351.54 | 0.21 ± 17.48 | 10ZT |
491.14 | 6.65 | 338.85 | 0.23 ± 17.41 | 15ZT |
510.79 | 6.85 | 324.79 | 0.38 ± 17.38 | 21ZT |
755.35 | 7.49 | 230.64 | 0.46 ± 15.44 | 80ZT |
736.55 | 7.16 | 210.00 | 0.48 ± 13.20 | 100ZT |
افزودن زیرکونیا به آلومینا تأثیر گسترده ای در افزایش استحکام شکست دارد در حالی که اثر آن بر روی چقرمگی شکست کمتر است.[۲۶] رابطه عکسی بین سختی و چقرمگی شکست وجود دارد.[۲۷] اگرچه میکروترک منجر به کاهش سختی میشود اما باعث بهبود چقرمگی میگردد.[۲۸] بنابراین این استحاله پذیری موجب کاهش در سختی است. چرا که سختی بهطور معکوس با استحاله فازی رابطه دارد.[۲۹][۳۰]
چقرمگی شکست[ویرایش]
حضور ترکیبی از شکستهای هم درون دانه ای و هم بین دانه ای منجر به چقرمگی بهتر نسبت به کامپوزیتهایی میشود که تنها حالت شکست بین دانه ای دارند. در این مورد، شکست بین دانه ای احتیاج به انرژی بیشتری نسبت به انتشار ترک در مقایسه با شکست بین دانه ای است. بنابراین منجربه بهبود چقرمگی میشود. تفاوتهای ریز ساختاری کامپوزیتها علت تفاوتهای رفتاری شکستشان است. ذرات بزرگ زیرکونیا که در طول مرز دانه قرار گرفته و ذرات بسیار کوچک در داخل دانههای آلومینا قرار میگیرند. این ریزساختار بین دانه ای دانههای آلومینا را تضعیف کرده و منجر به وجود آمدن انتشار ترک بین دانه ای میشود.[۳۱] با افزایش ذرات زیرکونیا در طول مرزدانهها، ترک در درون دانههای زیرکونیا به استثنای مرزدانههای آلومینا انتشار می یابد. بنابراین منجر به حالت شکست بین دانه ای میشود.[۲۷]
استحکام[ویرایش]
استحکام رابطه مستقیمی با مقدار زیرکونیا تتراگونال موجود در کامپوزیت زینتر شده دارد.[۳۲][۳۳] بنابراین استحکام زیاد در رابطه با مقدار زیاد فاز تتراگونال و استحکام کم در رابطه با مقدار زیاد فاز منوکلینیک است.[۳۴][۳۵] علاوه بر این تقویت کردن با زیرکونیا ناپایدار منجر به میکروترکهایی در حین سرد شدن میشود، بنابراین کاهش تدریجی در استحکام با افزایش کسر ذرات ناپایدار رخ میدهد.[۳۶][۳۷]
مدول یانگ[ویرایش]
به دلیل اینکه مدول یانگ زیرکونیا کوچکتر از مدول یانگ آلومینا است، مدول یانگ با افزایش مقدار زیرکونیا کاهش می یابد.[۳۸][۳۹] حضور تخلخلها باعث کاهش مدول یانگ کامپوزیتها میشود.[۳۸] مدول یانگ کامپوزیتهای ZTA که حاوی مقدار بالای زیرکونیا تتراگونال هستند از قانون خطی مخلوطها پیروی میکند. با این حال، با افزایش مقدار فاز منوکلینیک مقدار مدول یانگ کاهش می یابد.[۲۸][۳۳]
سختی[ویرایش]
افزودن زیرکونیا به آلومینا منجر به کاهش سختی کامپوزیت ZTA میشود. این اثر مرتبط با سختی کمتر زیرکونیا در مقایسه با زمینه آلومینا است.[۲۷][۴۰][۴۱] سختی ZTA حاوی زیرکونیا تتراگونال باقی مانده کمتر از آنهایی است که حاوی زیرکونیا منوکلینیک باشند.[۲۸]
کاربردها[ویرایش]
همان طور که در بخش معرفی توضیح داده شد دو دسته کامپوزیت بر اساس سیستم ZrO2-Al2O3 ساخته شدهاست: ۱. زیرکونیای تقویت شده با ذرات آلومینا(ATZ) و ۲. آلومینای چقر شده با زیرکونیا(ZTA) در مورد دسته دوم تحقيقات زيادي به منظور بررسي خواص و ريزساختار آنها انجام شدهاست اما زيركونیا حاوي ذرات آلومينا كمتر مورد بحث قرار گرفته و اطلاعات كمي در مورد آن در دسترس است. آلومینای چقرشده با زیرکونیا یک کامپوزیتهای دوتایی است که در آن زیرکونیا به زمینه آلومینا به عنوان یک فاز دوم اضافه شدهاست. این کامپوزیت به دلیل خواص مکانیکی عالی خود نظیرسختی، استحکام، چقرمگی بالا و مقاومت در برابر سایش بهطور گسترده برای کاربردهای مختلف ازقبیل قطعات سایشی،ابزار برش، کاربردهای بیوپزشکی استفاده میشود.[۴۲][۴۳][۴۴][۴۵][۴۶]
کاربرد های بیوپزشکی[ویرایش]
پیشرفتهای بزرگ در تکنیکهای ترمیم دندانها با استفاده از مواد سرامیکی از دهه 70 ایجاد شدهاست. که بهطور گسترده در ایمپلنتها استفاده میشود.(شکل۱)
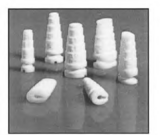
مواد سرامیکی، مزایای نسبی مانند زیبایی ظاهری دندان ترمیم شده بهتر، زیست سازگاری و مقاومت شیمیایی را نشان میدهد.[۴۷].
هم چنین علت اصلی شهرت و محبوبیت زیرکونیا، ساختار بلورین الماس شکل و عاری از فلز آن است که هنگام استفاده در دندانپزشکی، ایمپلنت اندکی تغییر میکند تا همرنگ دندان شود.[۴۷][۴۸]
اغلب بیماران به خاطر وجود جیوه موجود در برخی مواد پرکننده دندان مانند آمالگام [۱] و خطرات آن برای بدن از ایمپلنت دندان جلوگیری میکنند در حالی که استفاده از کامپوزیتهای آلومینا زیرکونیا هیچ فلزی را در ساختارخود ندارند و هم چنین هیچ گزارشی از آلرژی به ایمپلنتهای کامپوزیتی حاوی زیرکونیا نشدهاست، زیرا به خاطر انتقال گرمائی بسیار پائین درجه حرارت نامطلوب که باعث حساسیت میشود واقعاً موجود نمیباشد.
هم چنین مزایایی که کامپوزیتهای حاوی زیرکونیا در دندان پزشکی دارند جذب نور توسط آنها در مقایسه با فلزات است روکشهای دندانی حاوی زیرکونیا نور را ازخود عبور داده و باعث میشود که روکش هم رنگ دندان شوند در حالیکه روکشهایی از جنس فلزات نور را از خود عبور نداده و باعث تیرگی و کبودی ظاهری دندان میشوند.[۴۷]
از کاربرد دیگر بیوپزشکی کامپوزیت آلومینا زیرکونیا استفاده از آن در ارتوپدی است، که آلومینا که بخاطر پایداری شیمیایی، خنثی بودن زیست سازگاری و اصطکاک و مقاومت در برابر خواص سایشی در پروتز قسمت فوقانی مفصل ران استفاده شدهاست. با این حال اینها به دلیل چقرمگی شکست پایین در بارگذاری بسیار حساس هستند. زیرکونیا به شکل زیرکونیا تثبیت شده و به مقدار جزئی آلومینا را به یک ماده چقرمه تبدیل میکند، هم چنین بعد از پرداخت، زیرکونیا ظاهر زیبایی را فراهم میکند که این به علت فیزیولوژی بی اثر بودن این ماده است و مقاومت خمشی خوب ،چقرمگی و مدول یانگ پایین در مقایسه با آلومینای خالص است.[۴۹] که تبدیل از یک ساختارکریستالی تتراگونال به ساختار مونوکلینیک در طی تهیه این کامپوزیت اتفاق می افتد و به همین ترتیب مانع انتشار ترک میشود و به مواد، استحکام و چقرمگی را میدهد و به یک ماده مناسب در پروتز قسمت فوقانی ران تبدیل میکند.[۴۸][۴۹]
نوع زیرکونیا پایدار شده در کامپوزیتهای الومینا زیرکونیا برای کاربردهای پزشکی اهمیت بالایی دارد همانطور که گفته شده برای پایداری زیرکونیا تتراگونال در دما پایین از مواد پایدارکننده ای از جمله ایتریا و سریا استفاده میگردد. زیرکونیا تثبیت شده با ایتریا مقاومت در برابر پیری کمی دارد در واقع، ایتریا جای خالی آنیونی تولید میکند که نقش کلیدی در نرخ نفوذ آب و در نتیجه در پیری، بازی میکند. از طرفی مواد مورد استفاده در کاربردهای پزشکی نیاز به پایداری در طول عمر بالا (حدود 30 سال) در شرایط بدن انسان دارند یک راه جایگزین برای جلوگیری از مشکل پیری، جایگزینی ایتریا با سرایا است که دارای ساختار مولکولی همسان با زیرکونیا بوده و هیچ جای خالی ایجاد نمیکند و مقاومت به پیری بالاتری در اکثر شرایط محیطی از خود نشان میدهد و همچنین دارای چقرمگی شکست قابل توجه و بالایی است.[۵۰]
کاربرد در ابزار های برشی[ویرایش]
آلومینای خالص دارای تافنس پایین، استحکام مکانیکی پایینی و رسانایی گرمایی پایینی است.[۵۱] افزودن 2 تا 10 % زیرکنیا به آلومینا میتواند بهطور قابل توجهی تافنس و مقاومت به شوک حرارتی را بهبود دهد. این روش تقویت آلومینا بر اساس استحالهٔ آلوتروپیک و ایجاد فاز مونوکلینیک به وجود می آید. این استحاله با سرد شدن نمونه و افزایش حجمی رخ میدهد. اگر دانههای زیرکونیا بسیار ریز باشند(کوچک تر از 0.3 میکرون) و به خوبی در آلومینا پراکنده شده باشند، این استحاله موجب تشکیل نیروهای فشاری در زمینهٔ آلومینا میشود. وقتی یک ترک تشکیل میشود و گسترش می یابد، آزادسازی نیروهای فشاری که به دلیل اشاعهٔ ترک ایجاد میشود، موجب میشود تا فاز شبه پایدار تشکیل شده، به فاز مونوکلینیک تبدیل شود. این تبدیل با انبساط همراه است و موجب میشود تا با تشکیل نیروهای فشاری، اشاعهٔ ترک محدود گردد. این استحالهها موجب میشود تا در کل تافنس ماده بهبود یابد. سرامیکهای آلومینا-زیرکنیا به دلیل خواصی که هنگام تشکیل کامپوزیت حاصل میشود ضرورتاً برای برشکاری منقطع چدن و فولاد مورد استفاده قرار میگیرد.[۵۲]
کاربرد به عنوان ساینده[ویرایش]
دو ویژگی مهم مواد ساینده سختی و چقرمگی است. ترکیب این دو ویژگی مناسب بودن ساینده برای کاربرد خاص را تعیین میکند.[۵۳] اکسید آلومینیوم دارای دمای ذوب بسیار بالایی در حدود 2054 درجه سانتیگراد و از لحاظ شیمیایی بسیار پایدار است. این ویژگی باعث میشود تا از این ماده در کاربردهایی استفاده شود که در آن نیاز به تحمل دمایی بالاست. استحکام و مقاومت به سایش آلومینا در بین اکسیدها، از همه بالاتر است و از این رو باعث میشود تا این ماده به عنوان ساینده قرار گیرد.[۵۴]
زیرکونیا به واسطه تحول فازی تنشهای فشاری در سطح ایجاد نموده و به همین دلیل کاربردهای نوینی در ابزارهای برنده و مقاوم در برابر سایش پیدا کردهاست.[۵۴] چرخهای ساینده آلومینا/زیرکونیا هفت برابر بهتر از چرخهای آلومینای خالص کار میکنند. کاربرد آن به عنوان گلولههای بال میل، انواع قیچیهای برش و یا تیغههای برش در صنعت برش دهنده در صنعت کاغذ، هدایتکننده الیاف نساجی و بسیاری موارد دیگر متداول شدهاست. عمر بسیار زیاد و دوره کار طولانی مدت و فاصله زمانی استراحت کم این نوع ابزارها موجب جبران قیمت اولیه میشود.[۵۵]
کاربرد به عنوان دیرگداز[ویرایش]
زیرکونیای تثبیت شده به جهت نقطه ذوب بالا و خواص شیمیایی عالی به عنوان یک نسوز مناسب مطرح است. حضور ذرات زیرکونیای تثبیت نشده در نسوزهایی مانند آلومینا باعث افزایش مقاومت به سایش و مقاومت به شوک حرارتی شده و کاربرد آن را در مواردی چون شیرهای راهگاهی لغزنده در تجهیزات فرایند ریختهگری مداوم فولاد و یا نازلها و افشانکهای خروج مذاب در پاتیلهای میانی و سیتمهای کشویی پاتیلها امکانپذیر میکند. در حقیقت با تحول فازی، شبکه ای از ترکهای ریز شکل گرفته که باعث مهار رشد ترک اصلی میشود. در همین راستااز زیرکونیا در ساخت بوتههای ذوب فلز به خصوص ذوب فلزات گران بها و سوپر آلیاژ (مصرفی در پرههای توربین)، بوتههای چینی آزمایشگاهی و شیمیایی، نسوزهای مقاوم در برابر شوک حرارتی در آستر کورهها و پاتیلها، ابزارآلات کورههای پخت سرامیک استفاده میشود. محدودیت اصلی آن مقاومت کم در برابر حمله سربارههای بازی و اکسید آهن است.[۵۶]
کاربرد هوایی[ویرایش]
مواد سایشپذیر سرامیکی دارای مقاومت به اکسیداسیون بهتری نسبت به آلیاژهای فلزی هستند. بعلاوه لایه سرامیکی میتواند به عنوان پوشش سد حرارتی عمل کرده و درجه حرارت سیل را زیر دمای بحرانی فلز نگهدارد. سیلهای هوایی توربین با مواد سایشپذیر سرامیکی به عنوان قطعه سیل فعال، به صورت یک سری ریلهای موازی، که روی صفحه پشتبند سیل ماشینکاری شدهاند، هستند. ریلها با پوشش مواد سرامیکی متخلخل که به روش پاشش حرارتی رسوب داده میشوند، پر میشوند. شرکت Sulzer Metco یک روش ترکیبی ریختهگری دقیق و پاشش حرارتی را برای تولید این قطعات ابداع کردهاست.[۵۷]
دو ماده منتخب اصلی برای پوشش سرامیکی اکسیدهای آلومینیوم و زیرکونیم هستند که هر دو، تا دمای ۱۲۰۰ درجه سانتیگراد مناسب هستند. با توجه به نتایج آزمایش سایش، پوششهای سرامیکی متخلخل خواص سایشپذیری ضعیفی را از خود نشان دادهاند. به منظور جلوگیری از تخریب نوک پره توربین به خصوص برای روتورهای شرود دار در پیک درجه حرارت تقریباً ۱۴۰۰ درجه سانتیگراد یک لایه سرامیکی ثانویه با قابلیت سایشپذیری مناسب روی لایه اول اسپری میشود. استفاده از پوششهای سایشپذیر زیرکونیا نتایج خوبی در زمینه سایشپذیری، مقاومت به سایش، مقاومت به شوک حرارتی در موتورهای جت جدید از خود نشان داده است.[۵۸] که با ترکیب این دوماده و تهیه کامپوزیتی از آنها میتوان به خواصی دوپل از هر دو ماده دست یافت که امروزه استفاده از آنها گسترش یافتهاست.
جستارهای وابسته[ویرایش]
منابع[ویرایش]
- ↑ «Zirconia Toughened Alumina» (به انگلیسی). دریافتشده در ۲۰۱۸-۱۱-۱۵.
- ↑ Boutz, M. M. R.; Winnubst, A. J. A.; Hartgers, F.; Burggraaf, A. J. (1994). "Effect of additives on densification and deformation of tetragonal zirconia". Journal of Materials Science. 29 (20): 5374–5382. doi:10.1007/bf01171550. ISSN 0022-2461.
- ↑ Saha, A., and D. C. Agrawal (۱۹۹۸). «Microstructure development in hybrid sol–gel prepared Al2O3–ZrO2 composites». Journal of materials science letters. doi:10.1023/A:100660910.
- ↑ Summitt, Robert (1984-11). "Corrosion inhibitors—developments since 1980". Materials Science and Engineering. 67 (2): 255–256. ISSN 0025-5416.
{{cite journal}}
: Check date values in:|date=
(help) - ↑ Xiong, F; Manory, R.R (1999-12). "The effect of test parameters on alumina wear under low contact stress". Wear. 236 (1–2): 240–245. doi:10.1016/s0043-1648(99)00276-8. ISSN 0043-1648.
{{cite journal}}
: Check date values in:|date=
(help) - ↑ Collie, M. J (۱۹۸۰). «Corrosion inhibitors—developments since». Materials Science and Engineering. doi:10.1016/0025-5416(84)90058-2.
- ↑ Marchi, Juliana; Delfino, Carina S.; Bressiani, José C.; Bressiani, Ana H. A.; Marques, Márcia M. (2009-05-26). "Cell Proliferation of Human Fibroblasts on Alumina and Hydroxyapatite-Based Ceramics with Different Surface Treatments†". International Journal of Applied Ceramic Technology. 7 (2): 139–147. doi:10.1111/j.1744-7402.2009.02388.x. ISSN 1546-542X.
- ↑ Sequeira, S.; Fernandes, M.H.; Neves, N.; Almeida, M.M. (2017-01). "Development and characterization of zirconia–alumina composites for orthopedic implants". Ceramics International. 43 (1): 693–703. doi:10.1016/j.ceramint.2016.09.216. ISSN 0272-8842.
{{cite journal}}
: Check date values in:|date=
(help) - ↑ Osman, Reham; Swain, Michael (2015-03-05). "A Critical Review of Dental Implant Materials with an Emphasis on Titanium versus Zirconia". Materials. 8 (3): 932–958. doi:10.3390/ma8030932. ISSN 1996-1944.
- ↑ Senthil Kumar, A.; Raja Durai, A.; Sornakumar, T. (2004-01). "Development of alumina–ceria ceramic composite cutting tool". International Journal of Refractory Metals and Hard Materials. 22 (1): 17–20. doi:10.1016/j.ijrmhm.2003.10.005. ISSN 0263-4368.
{{cite journal}}
: Check date values in:|date=
(help) - ↑ ۱۱٫۰ ۱۱٫۱ GARVIE, R. C.; HANNINK, R. H.; PASCOE, R. T. (1975-12). "Ceramic steel?". Nature. 258 (5537): 703–704. doi:10.1038/258703a0. ISSN 0028-0836.
{{cite journal}}
: Check date values in:|date=
(help) - ↑ Rao, A.Srinivasa; Cannon, W.Roger (1989-01). "Alumina/zirconia composites produced from commercial alumina and synthesised hydrous zirconia". Ceramics International. 15 (3): 179–188. doi:10.1016/0272-8842(89)90014-x. ISSN 0272-8842.
{{cite journal}}
: Check date values in:|date=
(help) - ↑ Tuan, W.H.; Chen, R.Z.; Wang, T.C.; Cheng, C.H.; Kuo, P.S. (2002-12). "Mechanical properties of Al2O3/ZrO2 composites". Journal of the European Ceramic Society. 22 (16): 2827–2833. doi:10.1016/s0955-2219(02)00043-2. ISSN 0955-2219.
{{cite journal}}
: Check date values in:|date=
(help) - ↑ ۱۴٫۰ ۱۴٫۱ Casellas, D; Ràfols, I; Llanes, L; Anglada, M (1999-05). "Fracture toughness of zirconia–alumina composites". International Journal of Refractory Metals and Hard Materials. 17 (1–3): 11–20. doi:10.1016/s0263-4368(98)00064-x. ISSN 0263-4368.
{{cite journal}}
: Check date values in:|date=
(help) - ↑ Wang, T.C.; Chen, R.Z.; Tuan, W.H. (2004-05). "Effect of zirconia addition on the oxidation resistance of Ni-toughened Al2O3". Journal of the European Ceramic Society. 24 (5): 833–840. doi:10.1016/s0955-2219(03)00337-6. ISSN 0955-2219.
{{cite journal}}
: Check date values in:|date=
(help) - ↑ ۱۶٫۰ ۱۶٫۱ ۱۶٫۲ ۱۶٫۳ ۱۶٫۴ Wang, J.; Stevens, R. (1989-10). "Zirconia-toughened alumina (ZTA) ceramics". Journal of Materials Science. 24 (10): 3421–3440. doi:10.1007/bf02385721. ISSN 0022-2461.
{{cite journal}}
: Check date values in:|date=
(help) - ↑ Magnani, Giuseppe; Brillante, Aldo (2005-10). "Effect of the composition and sintering process on mechanical properties and residual stresses in zirconia–alumina composites". Journal of the European Ceramic Society. 25 (15): 3383–3392. doi:10.1016/j.jeurceramsoc.2004.09.025. ISSN 0955-2219.
{{cite journal}}
: Check date values in:|date=
(help) - ↑ Saha, A.; Agrawal, D. C. (1998). "Microstructure development in hybrid sol–gel prepared Al2O3–ZrO2 composites". Journal of Materials Science Letters (به انگلیسی). 17 (15): 1333–1336. doi:10.1023/a:1006609104115. ISSN 0261-8028.
- ↑ Lange, F. F. (۱۹۸۲). «Transformation toughening». Journal of Materials science. doi:10.1007/BF00809057.
- ↑ Ruf, H., and Anthony G. Evans (۱۹۸۳). «Toughening by monoclinic zirconia». Journal of the American Ceramic Society. doi:10.1111/j.1151-2916.1983.tb10042.x.
- ↑ جعفر جعفريپور ميبدي، يعقوب علّي ، صاحبعلي منافي و احمد هادي (۱۳۸۸). «ساخت و بررسي ريزساختار و خواص مكانيكي نانوكامپوزيت هاي آلومينا-زيركونيا». نانو مواد (تحقيقات مواد نانو كامپوزيتي). شاپا https://www.sid.ir/fa/journal/ViewPaper.aspx?FID=۶۰۰۰۱۱۳۸۸۰۴۰۸مقدار
|issn=
را بررسی کنید (کمک). - ↑ ۲۲٫۰ ۲۲٫۱ Sarkar, D.; Adak, S.; Mitra, N.K. (2007-01). "Preparation and characterization of an Al2O3–ZrO2 nanocomposite, Part I: Powder synthesis and transformation behavior during fracture". Composites Part A: Applied Science and Manufacturing. 38 (1): 124–131. doi:10.1016/j.compositesa.2006.01.005. ISSN 1359-835X.
{{cite journal}}
: Check date values in:|date=
(help) - ↑ جعفر جعفريپور ميبدی، يعقوب علّي ،صاحبعلي منافي و احمد هادي (۱۳۸۸). «ساخت و بررسي ريزساختار و خواص مكانيكي نانوكامپوزيت هاي آلومينا-زيركونيا». نانو مواد (تحقيقات مواد نانو كامپوزيتي). شاپا https://www.sid.ir/fa/journal/ViewPaper.aspx?FID=۶۰۰۰۱۱۳۸۸۰۴۰۸مقدار
|issn=
را بررسی کنید (کمک). - ↑ پور, حسین, خوارزمی; رنجبر, خلیل, (2015). "تاثیر افزودن اکسید کروم بررفتار تف جوشی و زیر ساختار Al2O3-10ZrO2". CIVILICA. 01.
{{cite journal}}
: نگهداری CS1: نقطهگذاری اضافه (link) - ↑ M. Cecilia, C. Nelson, J. Filho, L. Guimaraes, Mechanical properties of alumina-zirconia composites for ceramic abutments, Vol. 7, No. 4, (2004)
- ↑ N. Claussen. Fracture toughness o f AI2O3 with an unstabilised Zr02 dispersed phase, J. Am. Ceram. Soc. Vol. 59, 1-2 (1976)
- ↑ ۲۷٫۰ ۲۷٫۱ ۲۷٫۲ A. Arab, Z. A. Ahmad and R. Ahmad, "Effects of yttria stabilized zirconia (3Y-TZP) percentages on the ZTA dynamic mechanical properties," Int. Journal of refractory metals and Hard Materials,vol. 50. 2015.
- ↑ ۲۸٫۰ ۲۸٫۱ ۲۸٫۲ https://doi.org/10.1111/j.1151-2916.1982.tb09939.x
- ↑ https://doi.org/10.1016/j.compositesa.2006.01.005
- ↑ https://doi.org/10.1016/S0924-0136(03)00396-0
- ↑ https://doi.org/10.1016/j.matchemphys.2008.05.041
- ↑ https://doi.org/10.1111/j.1151-2916.1981.tb09555.x
- ↑ ۳۳٫۰ ۳۳٫۱ F. Lange, "transformation roughening, part 4: fabrication, fracture toughness and strength of Al2O3-ZrO2 composites," J. Mater. Sci., vol. 17, 1982.
- ↑ https://doi.org/10.1016/j.dental.2007.05.005
- ↑ http://dx.doi.org/10.1007/BF00719732
- ↑ https://doi.org/10.1111/j.1151-2916.1976.tb09386.x
- ↑ https://doi.org/10.1007/BF02385721
- ↑ ۳۸٫۰ ۳۸٫۱ W. Tuan, R. Chen, T. Wang, C. Cheng and P. Kuo,"Mechanical properties of Al2O3/ZrO2 Composites," Journal of the European Ceramic Society, vol. 22, 2002.
- ↑ https://doi.org/10.1016/j.ceramint.2005.02.012
- ↑ I. Ganesh, G. Sundararajan, S. Olhero and J. Ferreira, "influence of chemical composition on sintering ability of ZTA ceramics consolidated from freeze dried granules," Ceramics International, vol. 37, 2011.
- ↑ https://doi.org/10.1016/j.jeurceramsoc.2012.02.057
- ↑ D. Casellas, “Fracture Toughness of Alumina and ZTACeramics: Microstructural Coarsening Effects”, Journal of Materials Processing Technology, 143–144, 2003, 148–152
- ↑ N.A. Rejab, and A. Azhar, “The Relationship between Microstructure and Fracture Toughness of Zirconia Toughened Alumina (ZTA) Added With MgO and CeO2”, Intertional Journal of Refractory Metals and Hard Materials, 41, 2013, 522–530
- ↑ N.A. Rejab, and A. Azhar, “The Effects of CeO2 Addition on the Physical, Microstructural and Mechanical Properties of Yttria Stabilized Zirconia Toughened Alumina (ZTA)”, Intertional Journal of Refractory Metals and Hard Materials, 36, 2013, 162–166
- ↑ ] C.,Suryanarayana “Mechanical alloying and milling”, Progress in Materials Science., No. 46, 2001, PP. 1-184
- ↑ ] R. C. Fries, Handbook o f materials for medical devices ASM international, 1998 Chapter (1)
- ↑ ۴۷٫۰ ۴۷٫۱ ۴۷٫۲ M. Cecilia, C. Nelson, J. Filho, L. Guimaraes, Mechanical properties of alumina-zirconia composites for ceramic abutments, Vol. 7, No. 4, (2004) pp 643-649
- ↑ ۴۸٫۰ ۴۸٫۱ C. Piconi, G. Maccauro, F. Muratori, E. Branched Prever, Alumina and zirconia ceramics in joint replacements, Journal of Applied Biomaterials & Biomechanics, 1 (2003) pp 19-32
- ↑ ۴۹٫۰ ۴۹٫۱ T, Burg , O. Standard, http://www.materials.unsw.edu.au/news/biomed-s.pdf بایگانیشده در ۱۲ نوامبر ۲۰۱۸ توسط Wayback Machine. Materials for Biomedical Engineering, , 2001 Materials Science and Engineering, Student Notes,05-07-2005
- ↑ Khaskhoussi, Amani; Calabrese, Luigi; Bouaziz, Jamel; Proverbio, Edoardo (2017-09). "Effect of TiO 2 addition on microstructure of zirconia/alumina sintered ceramics". Ceramics International. 43 (13): 10392–10402. doi:10.1016/j.ceramint.2017.05.074. ISSN 0272-8842.
{{cite journal}}
: Check date values in:|date=
(help) - ↑ Wang, J.; Stevens, R. Review: Zirconia-toughened alumina (ZTA) ceramics. J. Mater. Sci. 1989, 34, 3421–3440.
- ↑ T. Sornakumar, a R. Krishnamurthy a & C. V. Gokularathnam b, Machining Performance of Phase Transformation Toughened Alumina and Partially Stabilised Zirconia Composite Cutting Tools, Department of Mechanical Engineering, h Department of Metallurgical Engineering, Indian Institute of Technology, Madras-600 036, India,31 May 1993
- ↑ Oxford, UK: Elsevier Advanced Technology,1993
- ↑ ۵۴٫۰ ۵۴٫۱ Casellas, D.; Ràfols, I.; Llanes, L.; Anglada, M. Fracture toughness of zirconia-alumina composites. Int. J. Refract. Meter. H 1999, 17, 11–20.
- ↑ Bartolomé, J.F.; Pecharromán Moya, J.S.; Martin, A.; Pastor, J.Y.; Llorca, J. Percolative mechanism of sliding wear in alumina/zirconia composites. J. Eur. Ceram. Soc. 2006, 26, 2619–2625.
- ↑ Zirconia. ویرایش 3rd ed. Oxford, UK: Elsevier Advanced Technology، 1993, ©1992. شابک ۱۸۵۶۱۷۱۸۱۷. OCLC ۲۸۵۴۹۶۹۰.
- ↑ «نسخه آرشیو شده». بایگانیشده از اصلی در ۱۳ نوامبر ۲۰۱۸. دریافتشده در ۲۵ نوامبر ۲۰۱۸.
- ↑ BA Kushner, AJ Rotolico, JE Nerz, LA Saia - US Patent 5,059,095, 1991 - Google Patents A rotor blade is for a gas turbine engine having a plurality of rotor blades and a substantially coaxial shroud encompassing the tips of the blades. A ceramic layer is bonded to the blade tip, the ceramic layer consisting of a combination of aluminum oxide and zirconium oxide or at least partially stabilized zirconium oxide. The ceramic layer is formed as a plasma sprayed coating or a high velocity oxy-fuel sprayed coating.